Keeping Decay at Bay
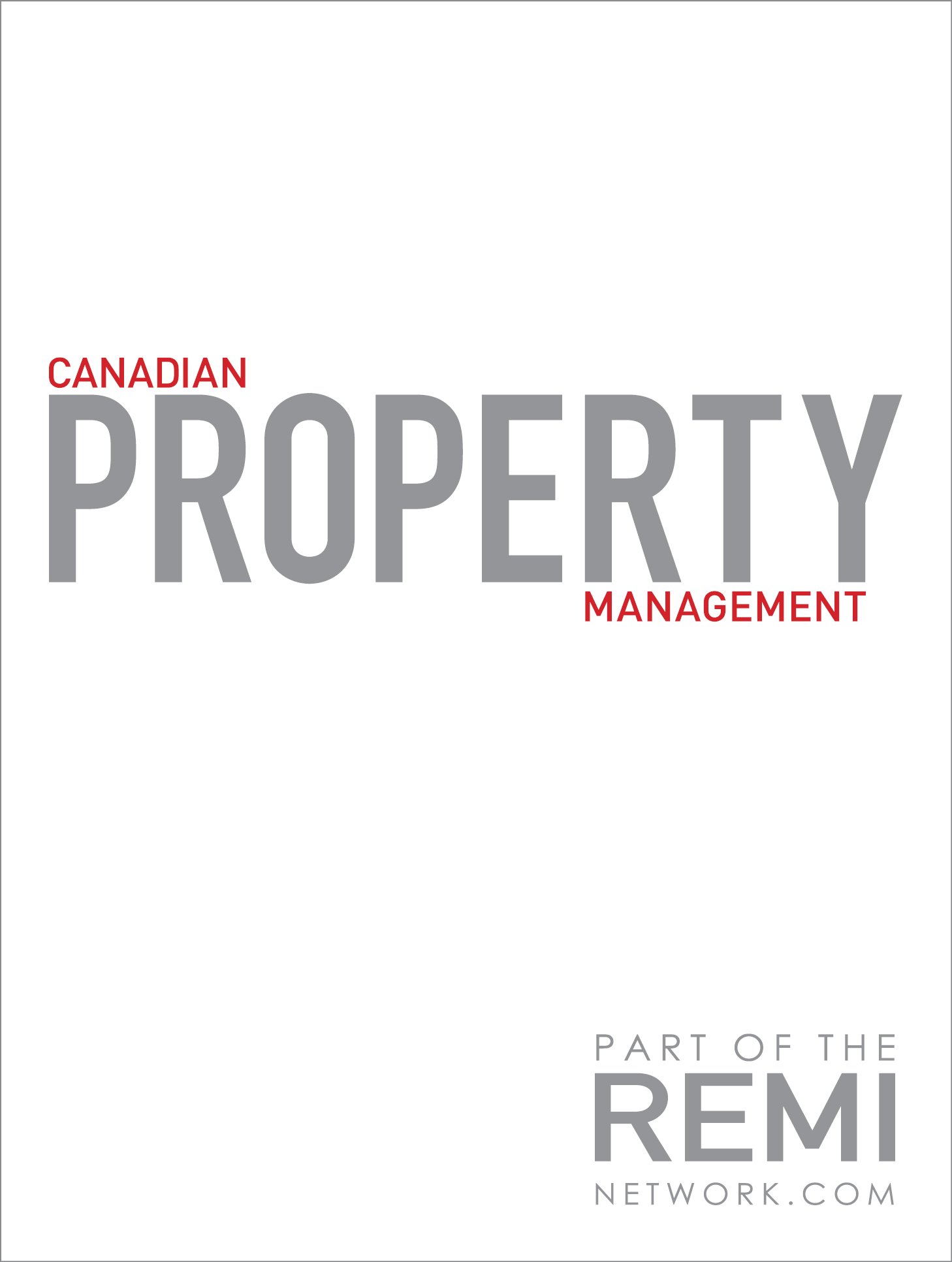
Canadian Property Management | August 2023
Bryant Bortolotto-Freeman, BSc., EIT
5 best practices for maximizing the service life of your traffic deck coating
If your building includes a parkade, chances are you’ve witnessed the wear and tear that comes from steady usage and exposure to moisture and contaminants like road salts. Even if the parking area is located indoors, the traffic deck coating (TDC) used to protect concrete surfaces will deteriorate over time, reducing its ability to effectively do its job.
“Traffic deck coating plays a key role in preserving concrete’s structural integrity, so it’s important to ensure it performs as intended,” said Bryant Bortolotto-Freeman, Engineer-in-Training at RJC Engineers. “By understanding the causes of concrete deterioration and following certain best practices to maximize your TDC, costly repairs to your concrete may be averted.”
What is Traffic Deck Coating?
A TDC is a multi-coat system formulated to protect concrete structures and structural elements from contact with moisture and contaminants. Typically, they are made up of a primer (polyurethane or epoxy-based), a basecoat, and a topcoat that work together to provide waterproofing protection, traction enhancements, wayfinding and light reflection in parkades and other concrete enclosures. Although usage of TDCs is widespread in North American, Bortolotto-Freeman has seen all-too often what happens when maintenance is ignored, or improper application creates weaknesses in the system. Common failures include debonding of the coating from the underlying substrate (or between the layers, cracks and scrapes letting in moisture, and surface damage from abrasion due to wheel racking and traffic exposure.
To prevent a failure and prolong the service life of your TDC, Bortolotto-Freeman recommends the following 5 Layers of Success:
Layer 1 – Surface Prep
Thorough surface preparation is crucial for a successful TDC installation, whether it’s brand-new concrete or an existing slab undergoing repairs. As such, shot blasting is an effective way to remove any micro-fractures, laitance, and provide the sound, open-textured surface area required for sufficient coating adhesion.